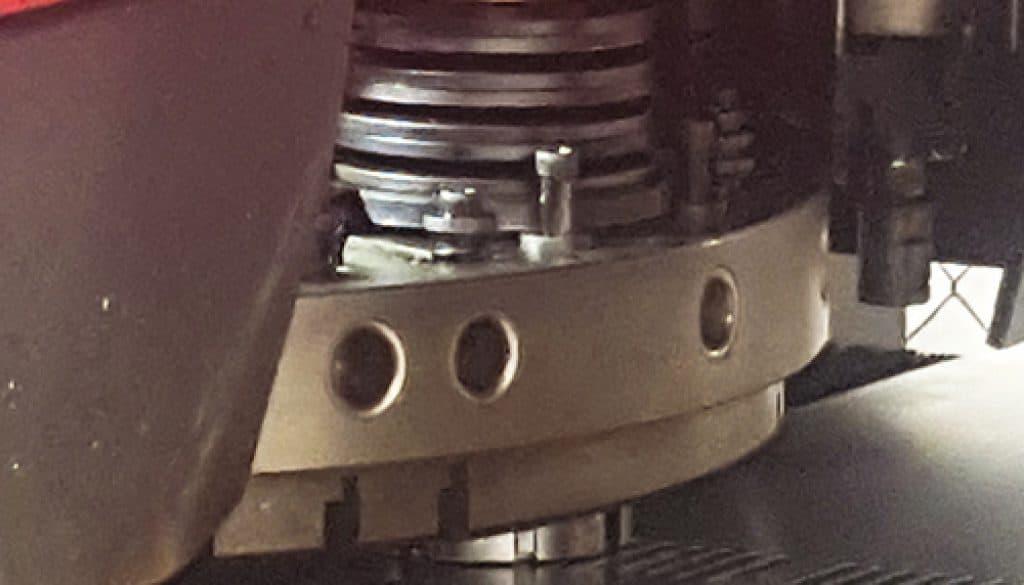
We form thousands of metal parts in our factory every day. One of the machines that we often use is our Amada Vipros 255 22 ton CNC turret punch press. This blog covers this machine and our process in more detail.
The Amada Vipros has a Fanuc 18P control. It has a 31 station turret, 3 auto index stations, a ball transfer table, and has a connected chiller. The machine is controlled by a CPU and software that connects to the machine. The Amada Vipros has a maximum hole diameter of 3.50”. This will vary depending on the material that we are punching.
Our process begins with a drawing of the part. The drawing will have been created during the design of the metal part. Once we have a final design and drawing, we upload the drawing to program the machine.
If we do not have the exact tooling required to punch the holes in the sheet metal, our in house tooling department will begin creating the tooling. This process is critical to ensuring that the ultimate product will meet specifications.
After the installation of tooling, and programming of the punch press, we can start to operate the press and create the holes in the sheet metal.
The next step will often involve bending the metal in secondary operations. We have a variety of press brakes available for this function. After that, we might weld the part to wire forms or other metal parts to create the final metal product. The final step will be applying the metal finish. See our blog here on metal finishes.
For more information on making metal parts or on metal fabrication, contact us now at [email protected].